I metodi di rivestimento del fotoresist sono generalmente suddivisi in rivestimento a rotazione, rivestimento a immersione e rivestimento a rullo, tra i quali il rivestimento a rotazione è il più comunemente utilizzato. Mediante il rivestimento a rotazione, il fotoresist viene gocciolato sul substrato e il substrato può essere ruotato ad alta velocità per ottenere una pellicola di fotoresist. Successivamente è possibile ottenere una pellicola solida riscaldandola su una piastra calda. Il rivestimento a rotazione è adatto per il rivestimento da film ultrasottili (circa 20 nm) a film spessi di circa 100 um. Le sue caratteristiche sono una buona uniformità, uno spessore uniforme della pellicola tra i wafer, pochi difetti, ecc. e la possibilità di ottenere una pellicola con elevate prestazioni di rivestimento.
Processo di rivestimento in rotazione
Durante il rivestimento in rotazione, la velocità di rotazione principale del substrato determina lo spessore del film del fotoresist. La relazione tra la velocità di rotazione e lo spessore del film è la seguente:
Spin=kTn
Nella formula Spin è la velocità di rotazione; T è lo spessore del film; k e n sono costanti.
Fattori che influenzano il processo di spin-coating
Sebbene lo spessore del film sia determinato dalla velocità di rotazione principale, è anche correlato alla temperatura ambiente, all'umidità, alla viscosità del fotoresist e al tipo di fotoresist. Il confronto tra diversi tipi di curve di rivestimento di fotoresist è mostrato nella Figura 1.
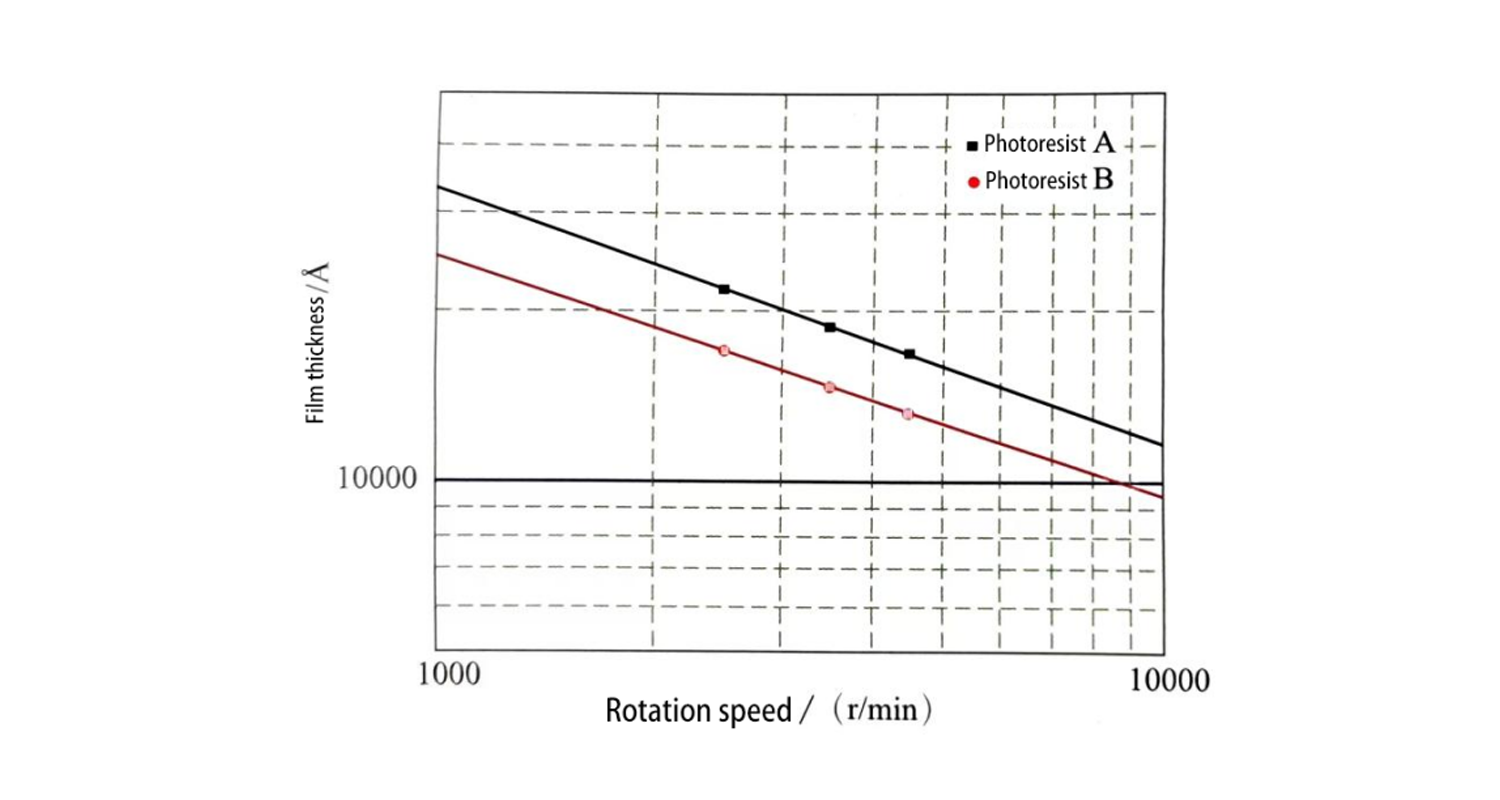
Figura 1: Confronto tra diversi tipi di curve di rivestimento di fotoresist
L'influenza del tempo di rotazione principale
Minore è il tempo di rotazione principale, maggiore è lo spessore del film. Quando si aumenta il tempo di rotazione principale, più sottile diventa la pellicola. Quando supera i 20s, lo spessore del film rimane pressoché invariato. Pertanto, il tempo di rotazione principale viene solitamente selezionato in modo che sia superiore a 20 secondi. La relazione tra il tempo di rotazione principale e lo spessore del film è mostrata nella Figura 2.
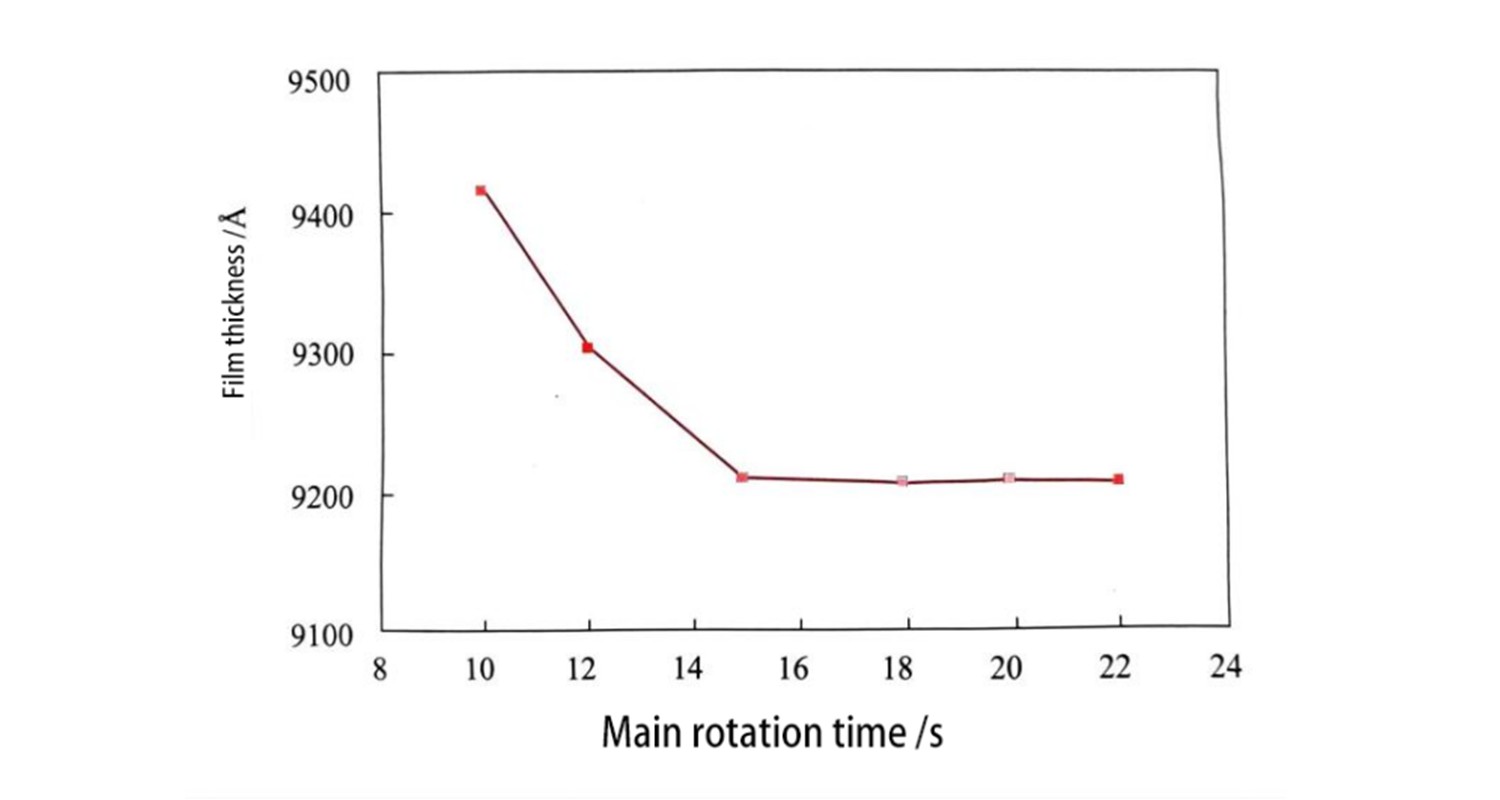
Figura 2: Relazione tra tempo di rotazione principale e spessore del film
Quando il fotoresist viene gocciolato sul substrato, anche se la successiva velocità di rotazione principale è la stessa, la velocità di rotazione del substrato durante il gocciolamento influenzerà lo spessore finale del film. Lo spessore del film di fotoresist aumenta con l'aumento della velocità di rotazione del substrato durante il gocciolamento, il che è dovuto all'influenza dell'evaporazione del solvente quando il fotoresist viene dispiegato dopo il gocciolamento. La Figura 3 mostra la relazione tra lo spessore del film e la velocità di rotazione principale a diverse velocità di rotazione del substrato durante il gocciolamento del fotoresist. Dalla figura si può vedere che all'aumentare della velocità di rotazione del substrato gocciolante lo spessore del film cambia più velocemente e la differenza è più evidente nella zona con velocità di rotazione principale inferiore.
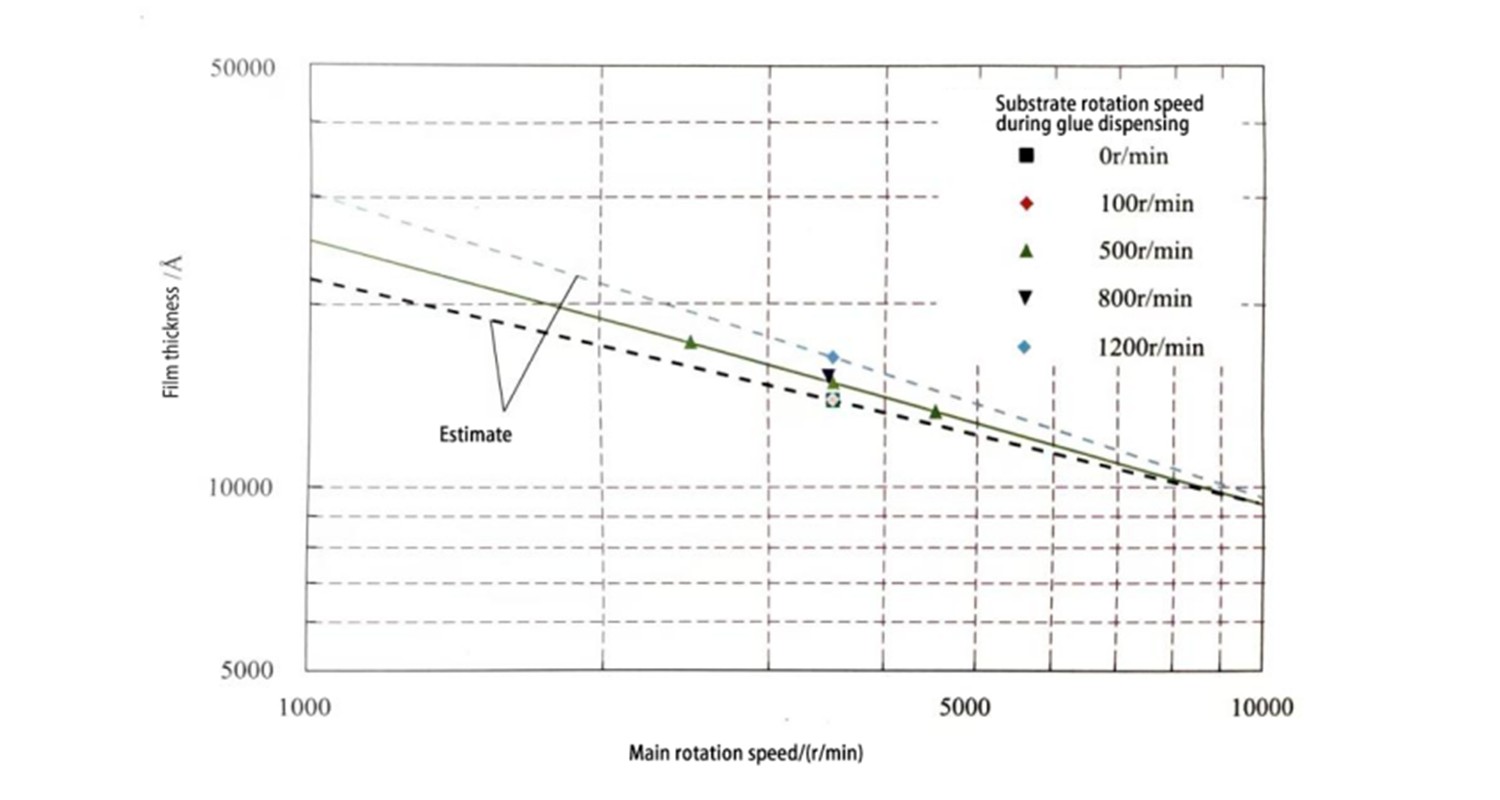
Figura 3: Relazione tra lo spessore della pellicola e la velocità di rotazione principale a diverse velocità di rotazione del substrato durante l'erogazione del fotoresist
Effetto dell'umidità durante il rivestimento
Quando l'umidità diminuisce, lo spessore del film aumenta, perché la diminuzione dell'umidità favorisce l'evaporazione del solvente. Tuttavia, la distribuzione dello spessore del film non cambia in modo significativo. La Figura 4 mostra la relazione tra umidità e distribuzione dello spessore del film durante il rivestimento.
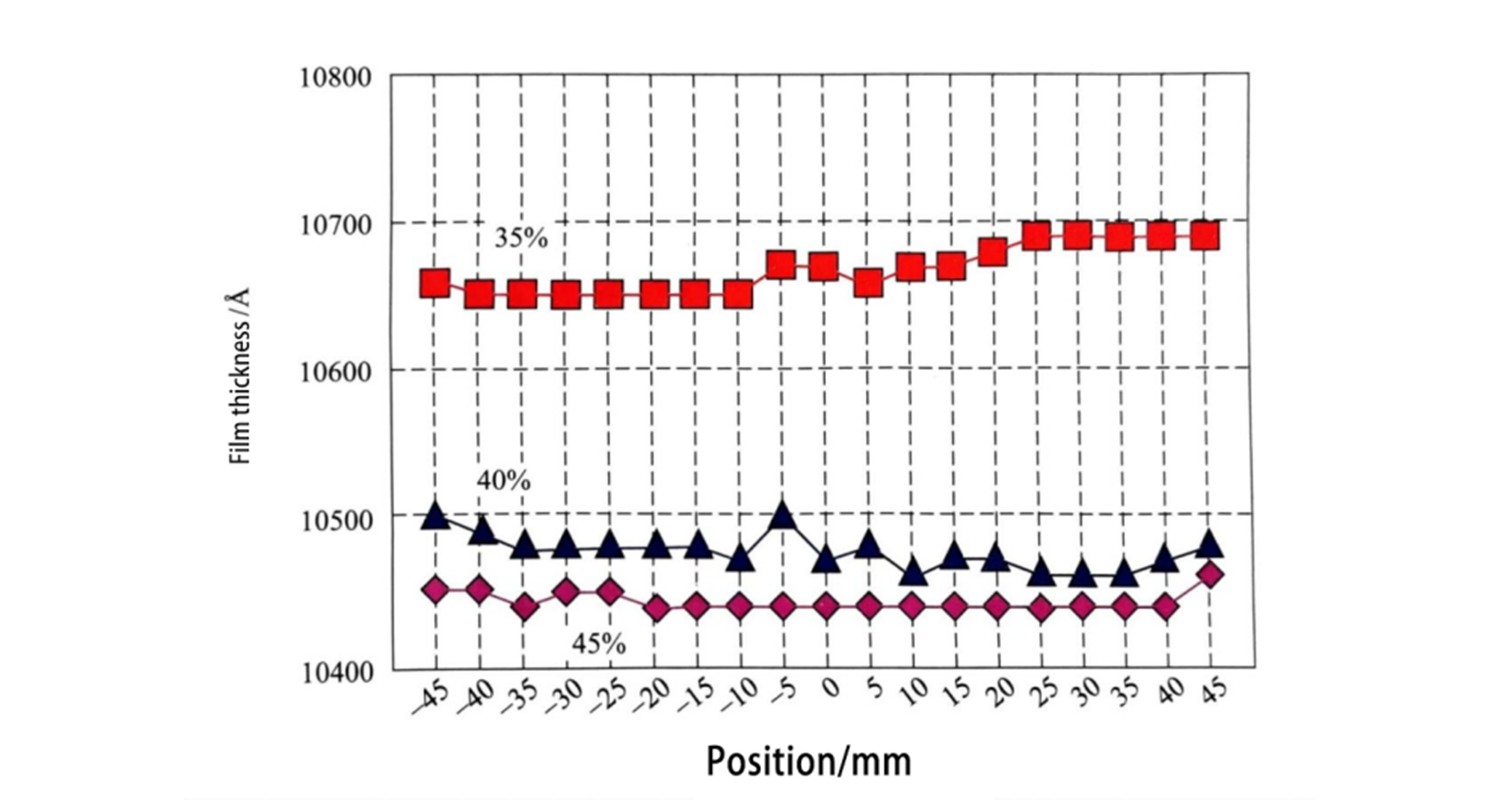
Figura 4: Relazione tra umidità e distribuzione dello spessore del film durante il rivestimento
Effetto della temperatura durante il rivestimento
Quando la temperatura interna aumenta, lo spessore del film aumenta. Dalla Figura 5 si può vedere che la distribuzione dello spessore del film di fotoresist cambia da convesso a concavo. La curva in figura mostra inoltre che la massima uniformità si ottiene quando la temperatura interna è di 26°C e la temperatura del fotoresist è di 21°C.
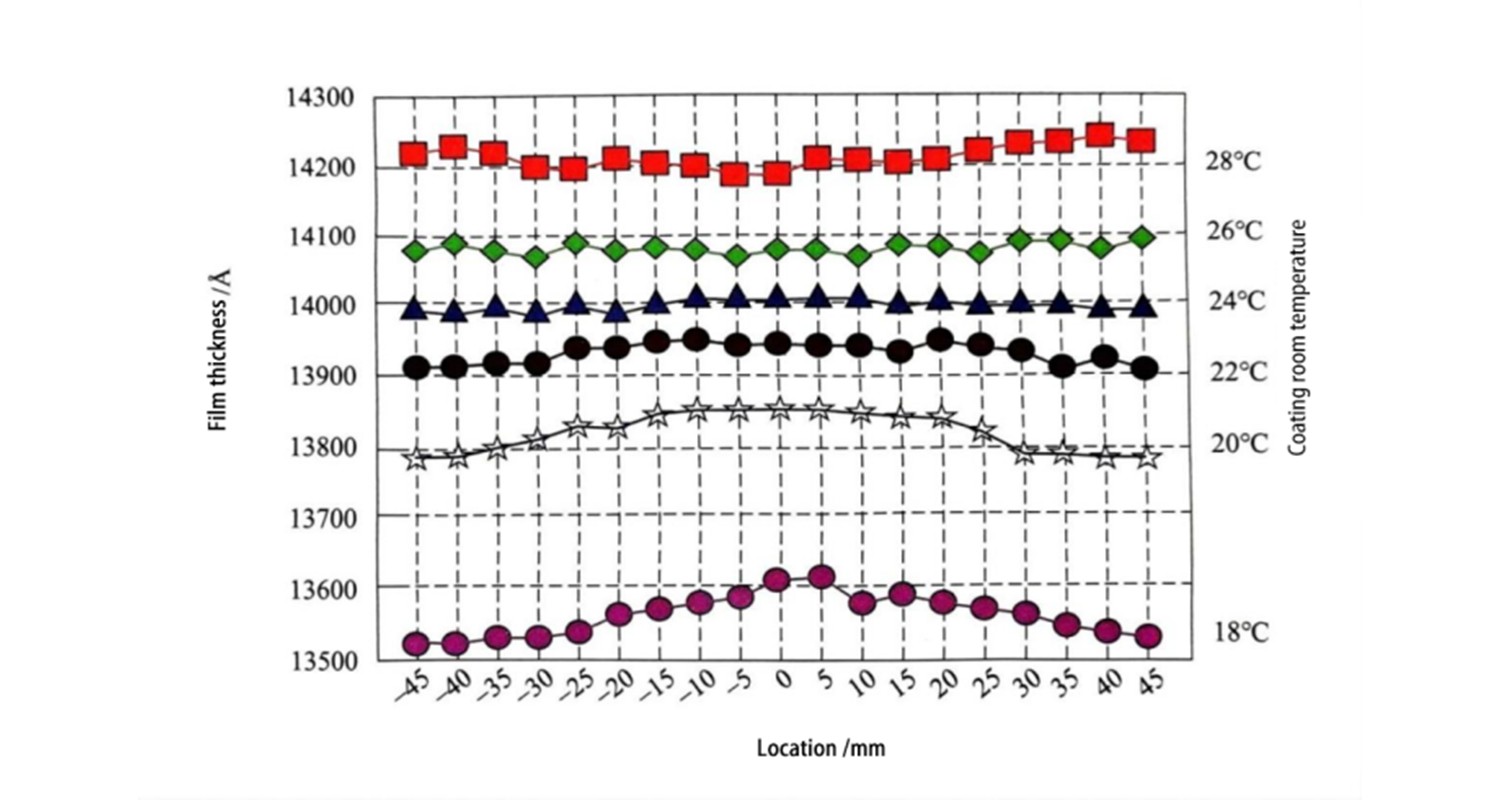
Figura 5: Relazione tra temperatura e distribuzione dello spessore del film durante il rivestimento
Effetto della velocità di scarico durante il rivestimento
La Figura 6 mostra la relazione tra la velocità di scarico e la distribuzione dello spessore del film. In assenza di scarico si evidenzia che il centro della cialda tende ad ispessirsi. Aumentando la velocità di scarico si migliorerà l'uniformità, ma se viene aumentata troppo l'uniformità diminuirà. Si può vedere che esiste un valore ottimale per la velocità di scarico.
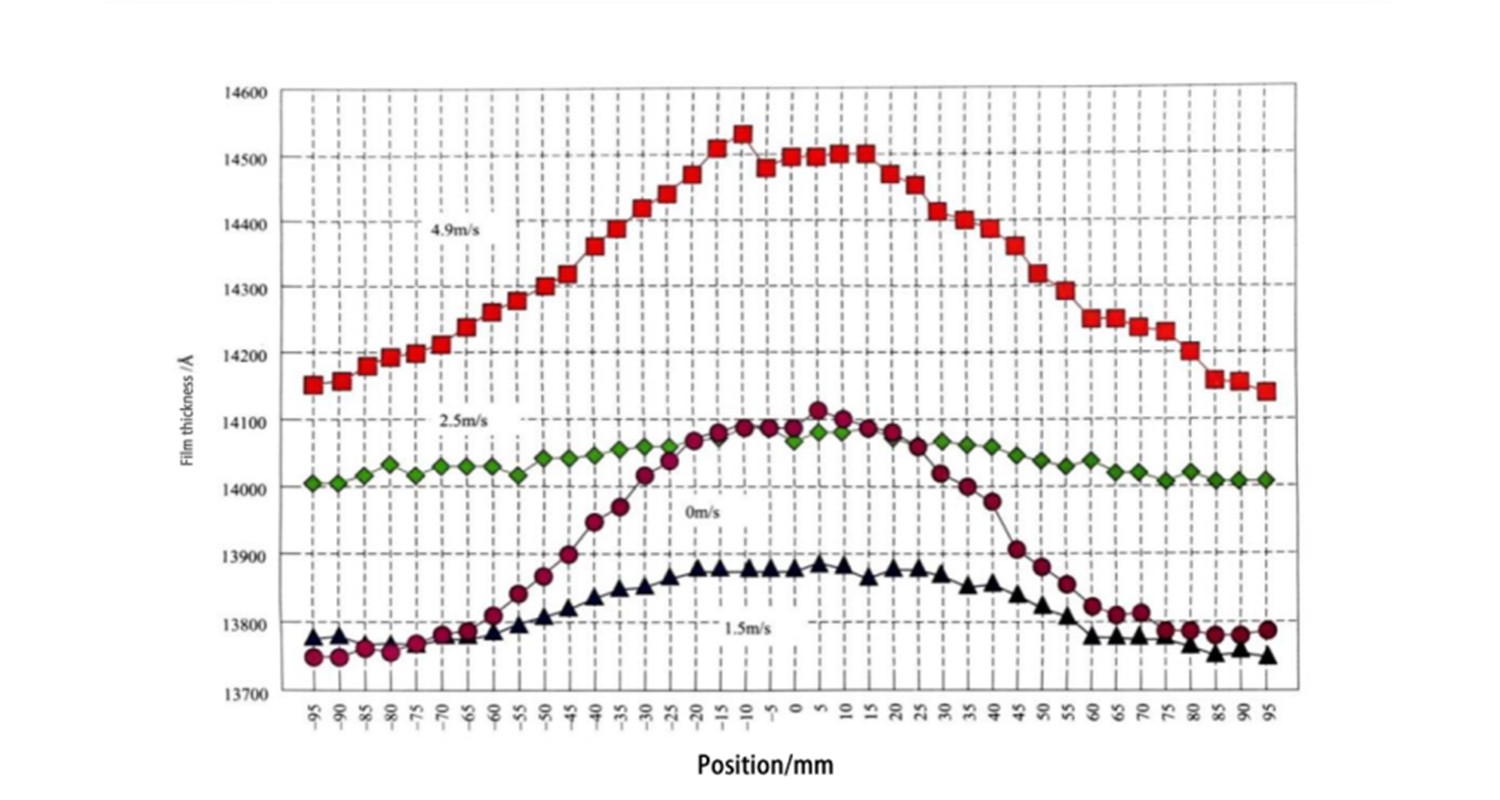
Figura 6: Relazione tra velocità di scarico e distribuzione dello spessore del film
Trattamento HMDS
Per rendere il fotoresist più rivestibile, il wafer deve essere trattato con esametildisilazano (HMDS). Soprattutto quando l'umidità è attaccata alla superficie della pellicola di ossido di Si, si forma silanolo, che riduce l'adesione del fotoresist. Per rimuovere l'umidità e decomporre il silanolo, il wafer viene solitamente riscaldato a 100-120°C e viene introdotta la nebbia HMDS per provocare una reazione chimica. Il meccanismo di reazione è mostrato nella Figura 7. Attraverso il trattamento HMDS, la superficie idrofila con un piccolo angolo di contatto diventa una superficie idrofobica con un ampio angolo di contatto. Il riscaldamento del wafer può ottenere una maggiore adesione del fotoresist.
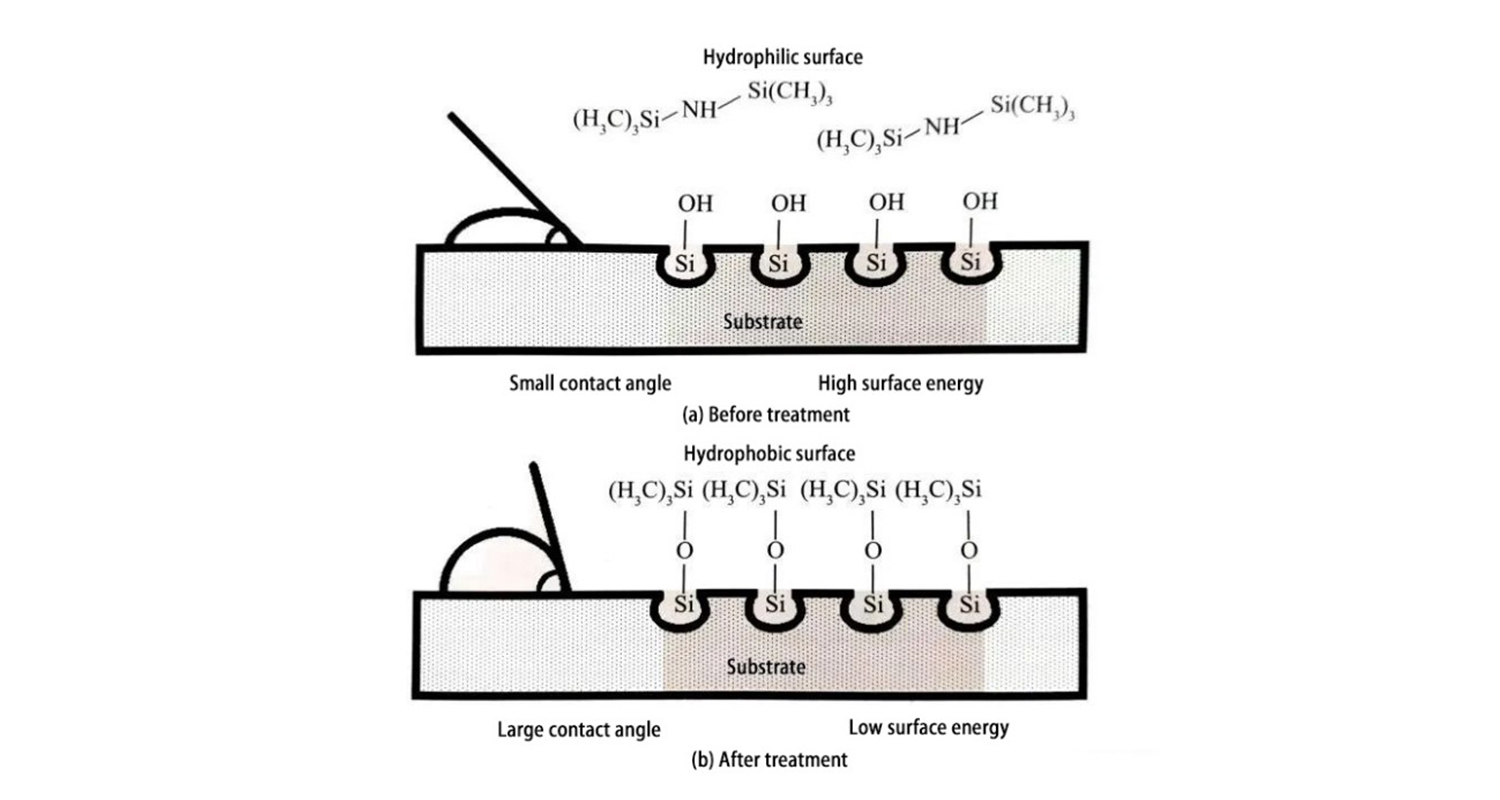
Figura 7: meccanismo di reazione HMDS
L'effetto del trattamento HMDS può essere osservato misurando l'angolo di contatto. La Figura 8 mostra la relazione tra il tempo di trattamento HMDS e l'angolo di contatto (temperatura di trattamento 110°C). Il substrato è Si, il tempo di trattamento HMDS è maggiore di 1 minuto, l'angolo di contatto è maggiore di 80° e l'effetto del trattamento è stabile. La Figura 9 mostra la relazione tra la temperatura di trattamento HMDS e l'angolo di contatto (tempo di trattamento 60 s). Quando la temperatura supera i 120 ℃, l'angolo di contatto diminuisce, indicando che l'HMDS si decompone a causa del calore. Pertanto, il trattamento HMDS viene solitamente eseguito a 100-110 ℃.
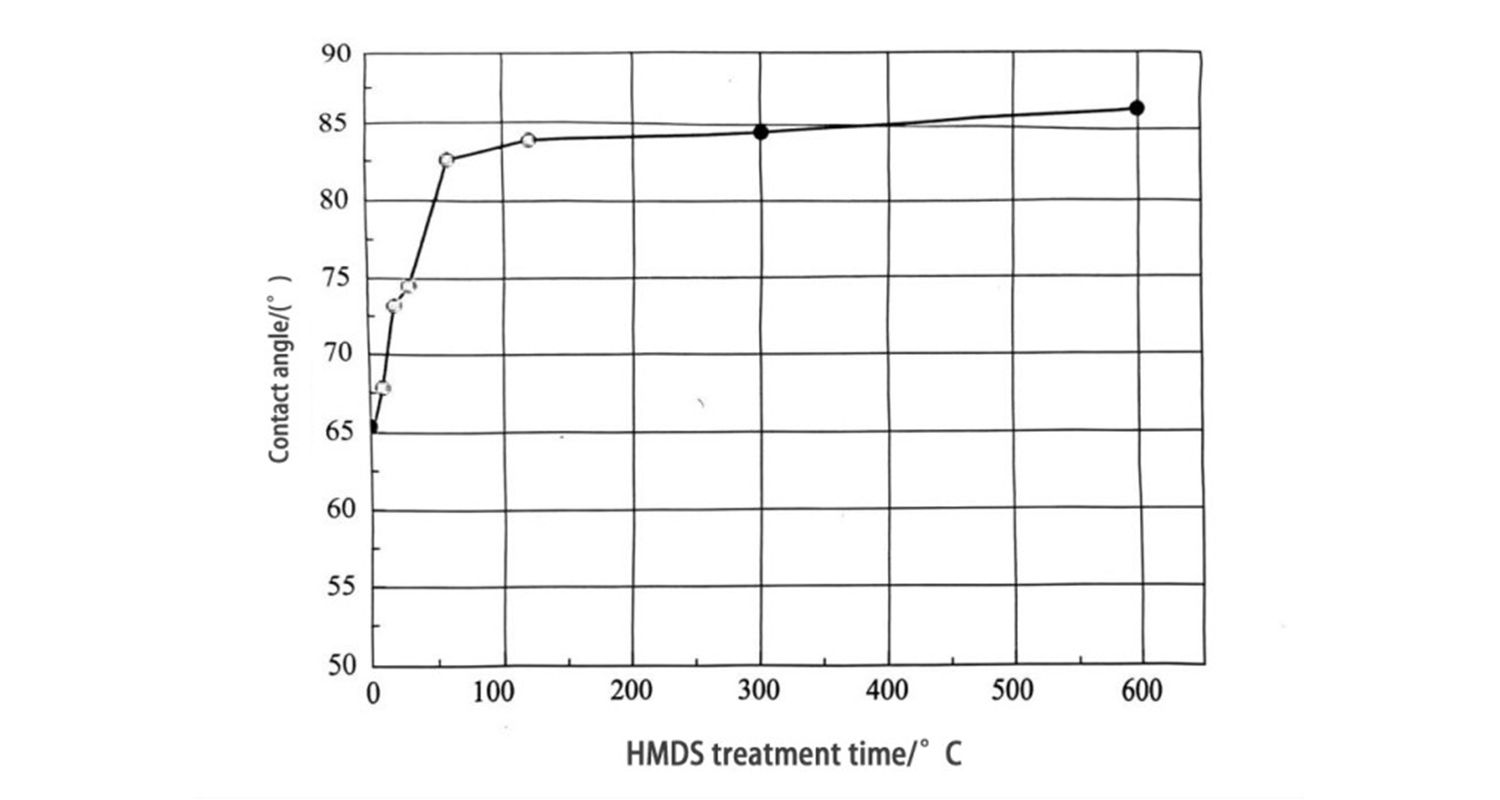
Figura 8: relazione tra il tempo di trattamento HMDS
e angolo di contatto (temperatura di trattamento 110 ℃)
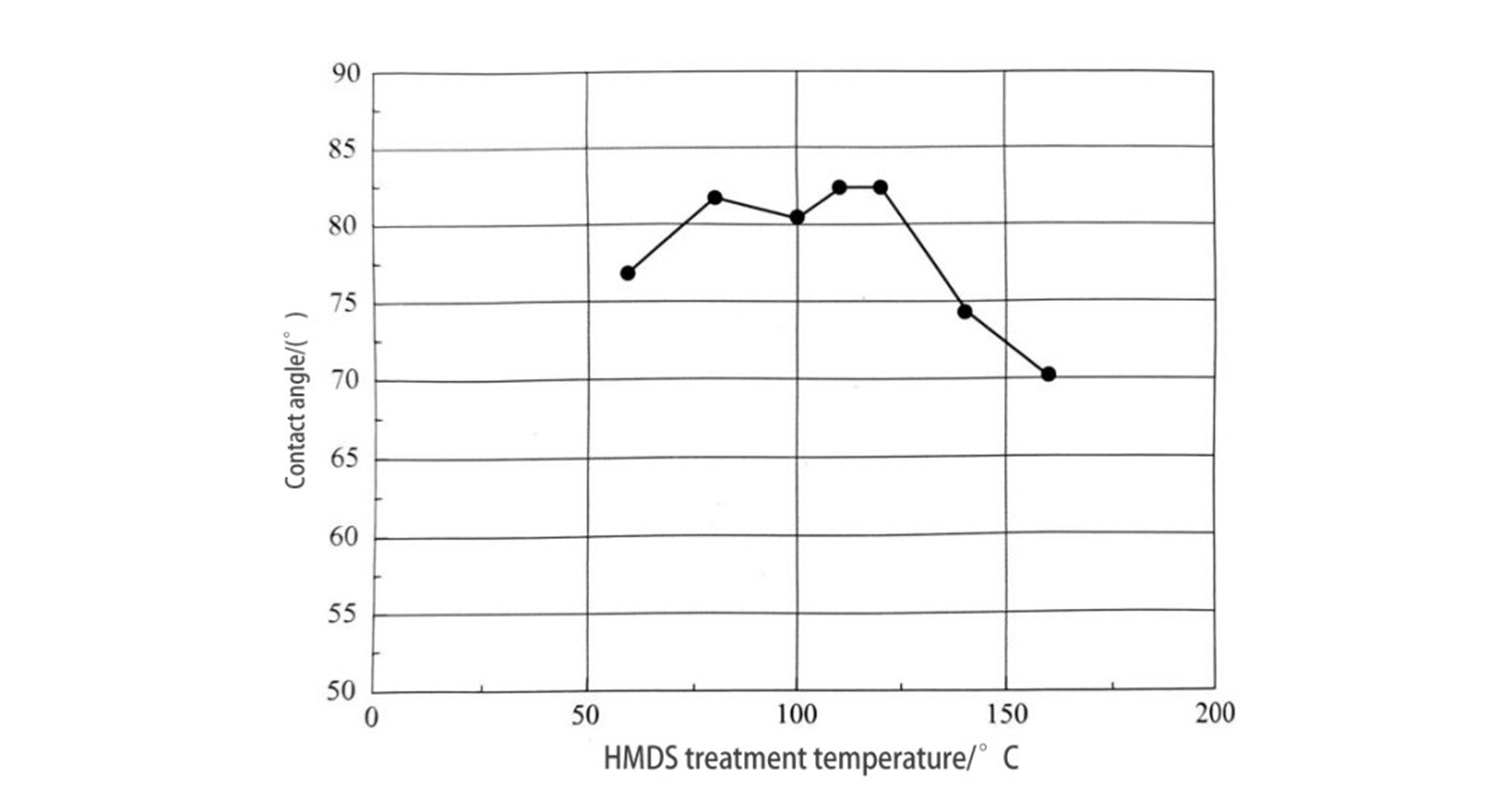
Figura 9: Relazione tra la temperatura del trattamento HMDS e l'angolo di contatto (tempo di trattamento 60 s)
Il trattamento HMDS viene eseguito su un substrato di silicio con una pellicola di ossido per formare un modello di fotoresist. La pellicola di ossido viene quindi attaccata con acido fluoridrico con l'aggiunta di un tampone e si è scoperto che dopo il trattamento HMDS, è possibile evitare che la struttura del fotoresist cada. La Figura 10 mostra l'effetto del trattamento HMDS (la dimensione del modello è 1um).
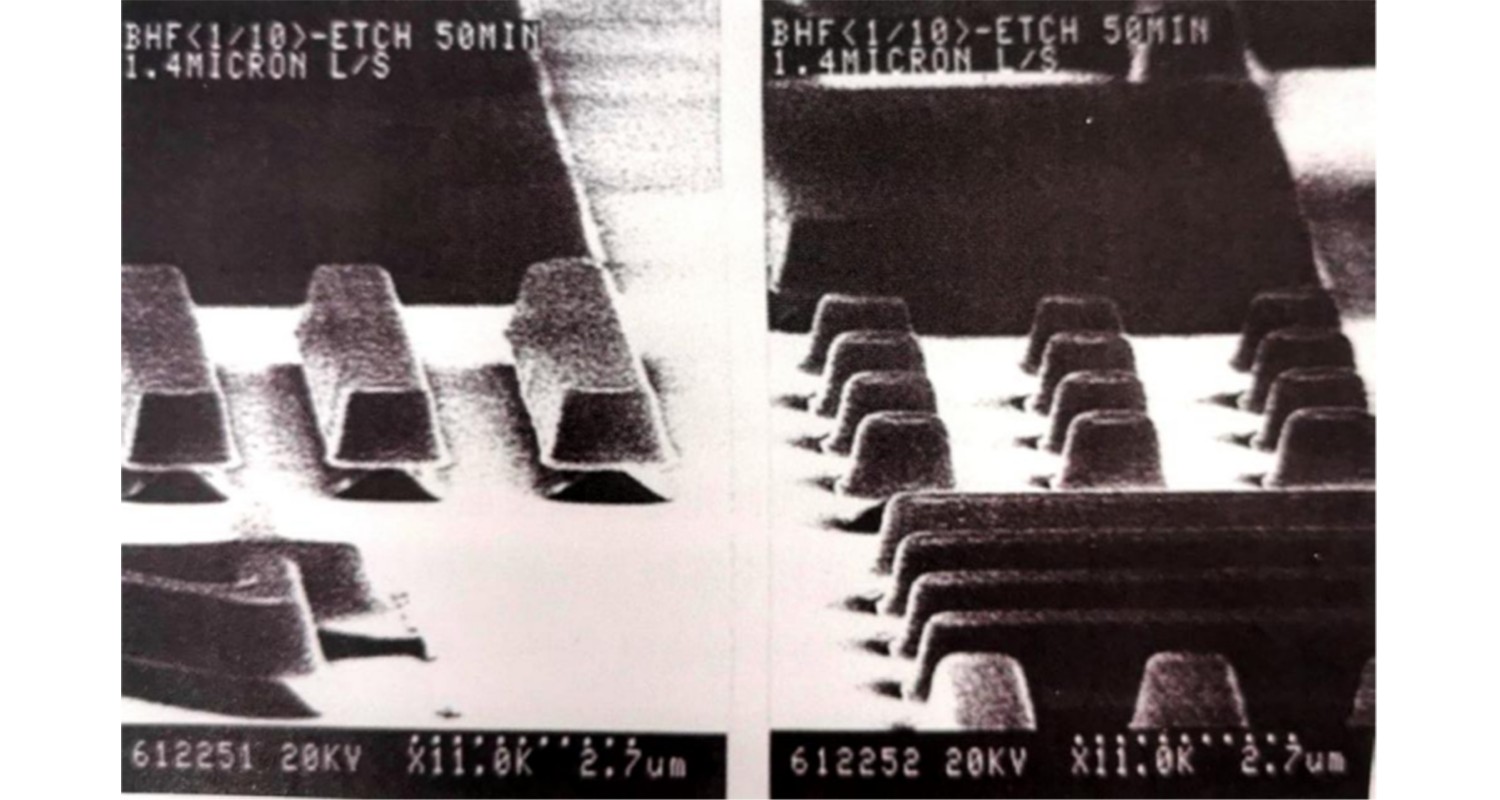
Figura 10: effetto del trattamento HMDS (la dimensione del modello è 1um)
Precottura
Alla stessa velocità di rotazione, maggiore è la temperatura di precottura, minore è lo spessore del film, il che indica che maggiore è la temperatura di precottura, maggiore è la quantità di solvente che evapora, risultando in uno spessore del film più sottile. La Figura 11 mostra la relazione tra la temperatura di precottura e il parametro A di Dill. Il parametro A indica la concentrazione dell'agente fotosensibile. Come si vede dalla figura, quando la temperatura di precottura sale oltre i 140°C, il parametro A diminuisce, indicando che l'agente fotosensibile si decompone ad una temperatura superiore a questa. La Figura 12 mostra la trasmittanza spettrale a diverse temperature di precottura. A 160°C e 180°C si può osservare un aumento della trasmittanza nell'intervallo di lunghezze d'onda di 300-500 nm. Ciò conferma che l'agente fotosensibile viene cotto e decomposto ad alte temperature. La temperatura di precottura ha un valore ottimale, che è determinato dalle caratteristiche della luce e dalla sensibilità.
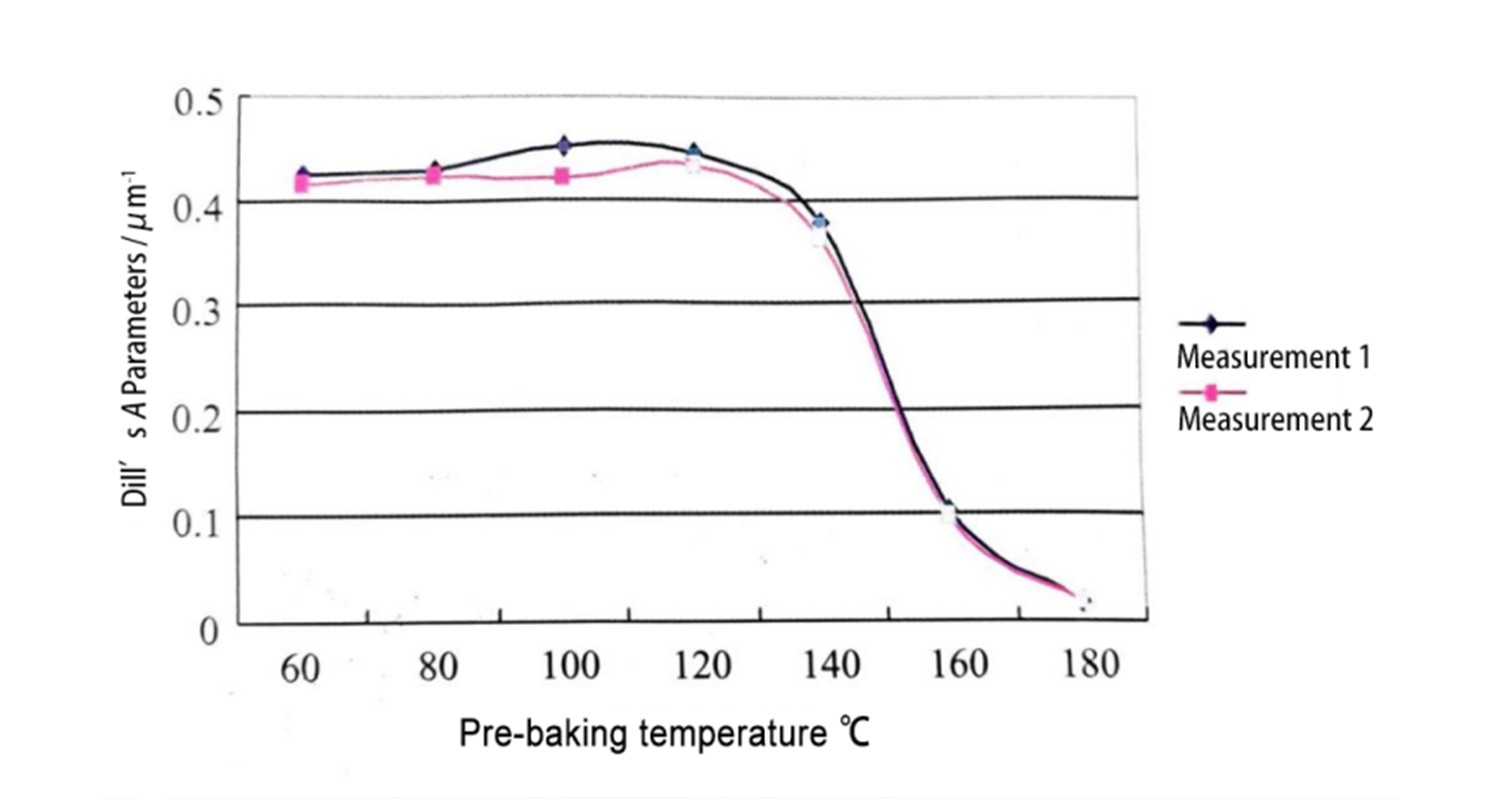
Figura 11: Relazione tra la temperatura di precottura e il parametro A di Dill
(valore misurato di OFPR-800/2)
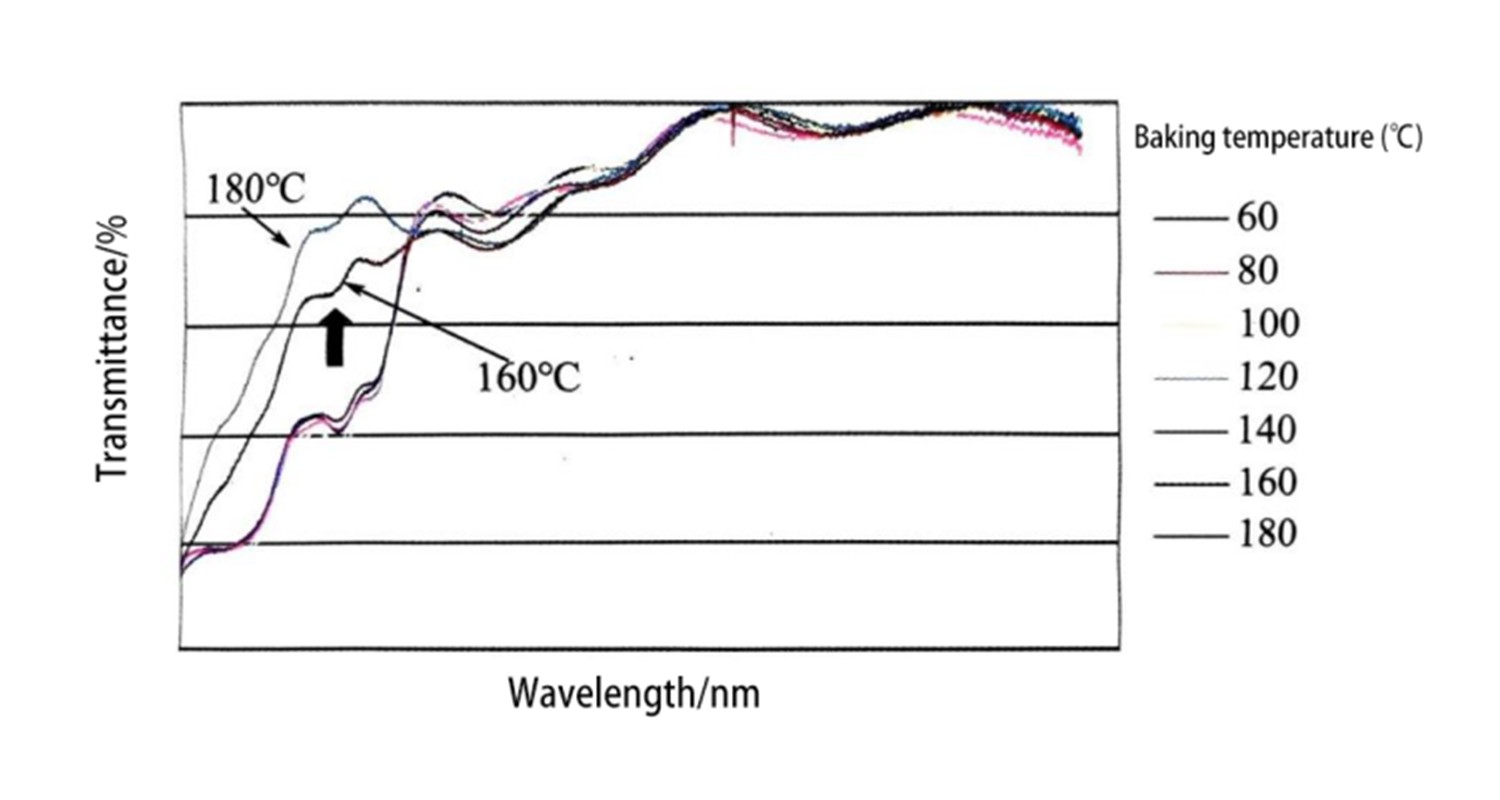
Figura 12: Trasmittanza spettrale a diverse temperature di precottura
(OFPR-800, spessore film 1um)
In breve, il metodo di rivestimento a rotazione presenta vantaggi unici come il controllo preciso dello spessore del film, prestazioni ad alto costo, condizioni di processo blande e funzionamento semplice, quindi ha effetti significativi nella riduzione dell’inquinamento, nel risparmio energetico e nel miglioramento delle prestazioni in termini di costi. Negli ultimi anni lo spin-coating ha acquisito sempre maggiore attenzione e la sua applicazione si è progressivamente diffusa in diversi ambiti.
Orario di pubblicazione: 27 novembre 2024